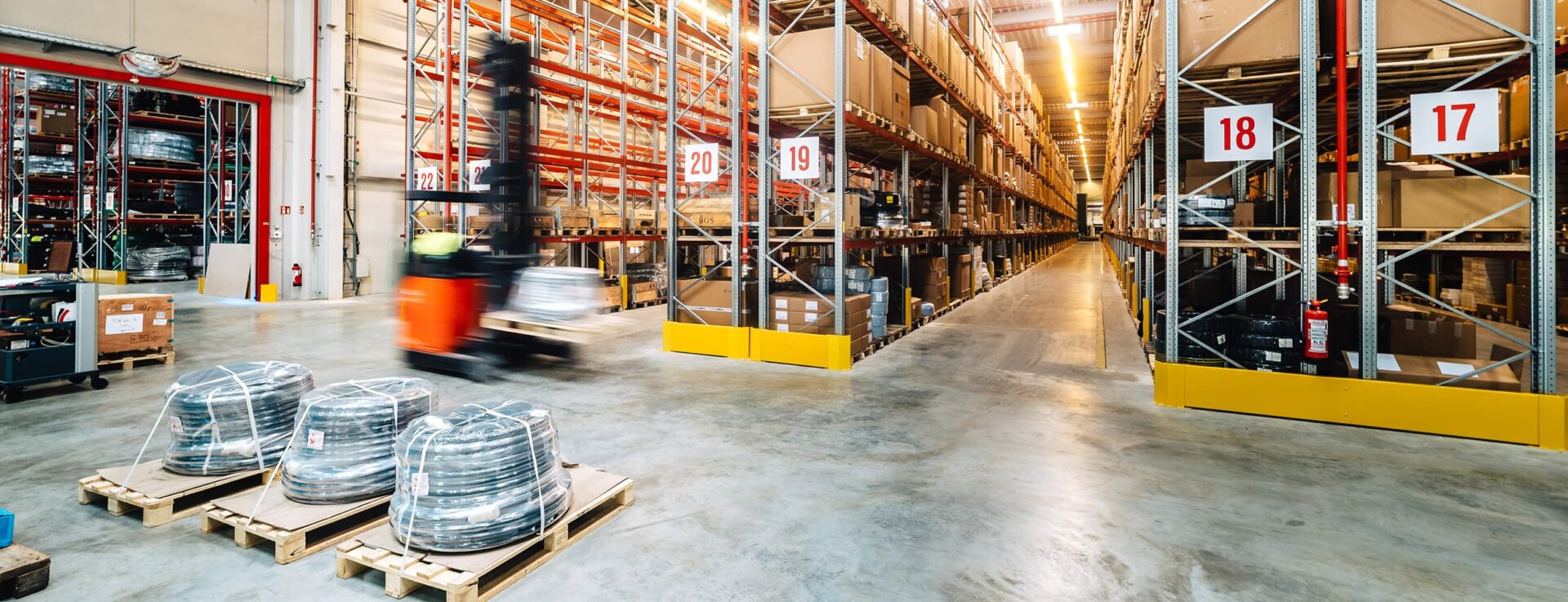
Optimal warehouse management with hansa‑flex
As your system partner for everything to do with fluid technology, our goal is to reduce the time you spend on routine business activities, so that you can concentrate on value-creating activities. Our services include supporting you in systematically optimising your warehousing processes to reduce unnecessary time spent searching for items and to design a more efficient material flow. Working with you, we find the solution that best matches your requirements.
Efficient ordering and warehousing processes
We are not only a reliable supplier of components, we also support you with our experience and specialist knowledge, always with the aim of increasing the profitability of your ordering and warehousing processes.
Optimising your inventory
We create and maintain a standardised article list for you. The list forms the basis for efficient warehouse management. The article list defines the ongoing use of material and enables the efficient use of your storage areas. We identify all the material groups you require to ensure a smooth production flow. As a one-stop provider, we can reliably supply you with the defined standard material. This allows you to consolidate your supplier list and save administration costs when ordering goods. With HANSA‑FLEX, you can choose flexible delivery intervals to suit your developing needs.
Proper storage of components
Component should be stored so that their quality and shelf-life are not adversely affected by dust, liquids or large temperature fluctuations. The risk of mechanical damage to components due to objects falling or rolling onto them should be minimised. Our highly capable employees are always available to provide advice and practical assistance to support you with their vast practice-proven knowledge and skills. These include, for example, the systematic positioning of warehousing systems and goods to shorten the distances your employees have to walk and the time they spend searching for the required items. This ensures there is nothing left to interfere with accessibility to components and machines.
Solutions for high goods throughput
Larger companies require correspondingly more parts and having automated ordering and warehousing processes becomes more important. There comes a point when written recording of material requirements and manual entry of orders takes up too much time for the whole process to remain efficient. Speak with your usual HANSA‑FLEX customer adviser about your options for digitalising your ordering processes, for example with a scanner solution, or automating them with a kanban system. Another possible way of optimising a high goods throughput would be to adopt a kit approach to your stock of parts.
Customer-focused warehouse management with hansa‑flex
We guarantee the availability of goods for you and offer you proactive support to design the associated processes to be as convenient and profitable as possible for you.
Reduced storage and material costs
Efficient warehouse management can minimise your tied-up capital and scrapped parts.
Substantial time savings
Shorter walking distances, reduced administration costs for orders and no wasted time searching, thanks to systematic optimisation.
Everything from a single source
HANSA‑FLEX is your reliable one-stop shop for all required components.
Digital solutions
We prepare the way and provide the equipment for your digitalised warehouse.
The perfect service package for every company
HANSA‑FLEX offers an expansive range of services, all flexibly adjustable to your requirements so that the overall solution is perfect for your company.
Other services for warehousing and logistics
Scanner solutions
Yes, we scan! Scanner solutions from HANSA‑FLEX enable you to determine your goods requirement for fluid technology in the warehouse or on…
Find out moreKitting
As a system partner, HANSA‑FLEX provides ready-to-install kits containing components from third-party supplies as well as from HANSA‑FLEX. The production…
Find out moreKanban delivery
HANSA‑FLEX offers kanban delivery as part of an optimally configured, customised logistics system. Delivery based on the kanban principle is very…
Find out more