HANSA-FLEX intensifies its partnership with Siemens Energy
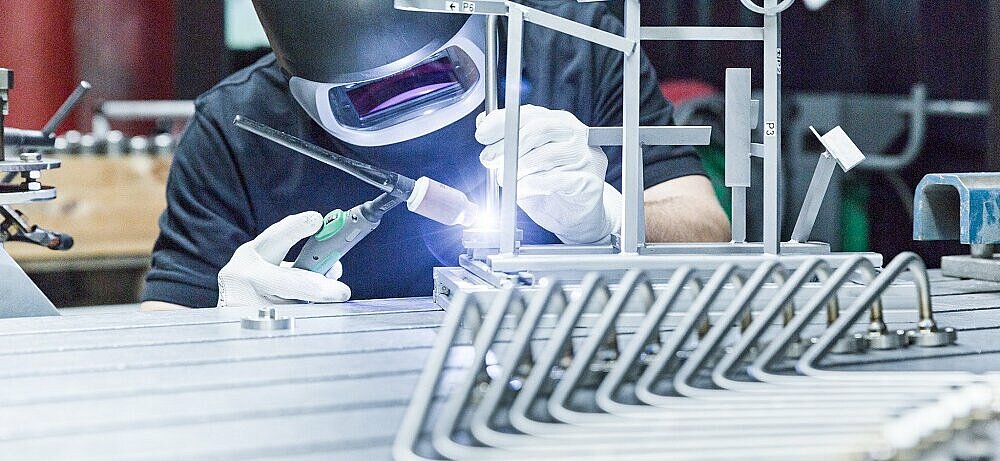
12.03.2024
Great expectations
It’s one of Berlin’s biggest future projects: In the form of Siemensstadt 2.0, a modern urban development that combines working, research and residential facilities is being created on the approximately 70-hectare Siemens industrial site in Berlin-Spandau. In addition to urban production facilities, research centres and office space for established companies and start-ups, there are plans for flats, student apartments and communal facilities. Some of the existing buildings will be retained, while a number of production locations will have to make way. As part of this project, Siemens Energy has outsourced pipe production for its electrical switchgear to HANSA‑FLEX.
Switchgear is used, for example, in transformer stations where high voltage is transformed into low voltage. “This transformation is necessary because electricity is transmitted at high voltage over long transport routes because of the lower power loss, while end consumers are supplied with low voltage”, explains Lars Wassermann, Product Engineer and Project Manager at Siemens Energy. The task of the circuit breakers is to disconnect the grid from the voltage supply in the event of faults, such as an overload or short circuit. Starting this year, HANSA‑FLEX will be supplying gas pipelines made of copper, brass and stainless steel with an external diameter of 6 to 22 mm and matching fittings for more than 100 component groups used in the circuit-breakers and for customised solutions.
For more than 100 assemblies used in circuit-breakers, HANSA‑FLEX supplies gas piping made of copper, brass and stainless steel from 6 to 22 mm outside diameter, as well as matching fittings.
Insulated by gas
The HANSA‑FLEX piping is installed in the support base of the single or three-pole encapsulated circuit breakers, and forms a continuous gas chamber containing the inert gas sulphur hexafluoride (SF6). “Due to its high electrical stability and high thermal conductivity, it is ideally suited for insulating the electrical conductors”, explains Wassermann. In addition, the gas plays a central role in extinguishing the arc that is created when the current flow is interrupted. As the distance between the switching contacts during the separation process is not yet sufficient for insulation, a voltage flash-over, the so-called ‘arc’, occurs briefly. “Due to the self-compression principle, a gas flow is generated in the breaker units when the contacts open”, is how Wassermann sums up the process patented by Siemens in 1973. “This increases the dielectric strength in the area of the contact opening, so that the arc is extinguished at shorter distances than, for example, is the case with air-insulated switches.”
Tested for safety
With voltages from 72.5 to 1,200 kilovolts, safety is the top priority. Siemens Energy, therefore, carries out comprehensive type tests in which the switches are continuously switched 10,000 times, iced or heated up by the supply of electricity. The final quality control for each switch is carried out as part of the all-round routine test. The pipes are also subjected to comprehensive testing: “We carry out regular routine tests to ensure that they are leak-proof”, explains Ralph Berge, Head of Production Area Projects at HANSA‑FLEX. Because the SF6 gas used has a very high greenhouse effect, both manufacturers and operators of circuit breakers are subject to strict regulations. “With a gas loss rate of 0.1 % per year, Siemens Energy is far below the limit prescribed by the International Electrotechnical Commission”, reports Wassermann.
Right on track
When planning its requirements, Siemens Energy determines in advance when individual pipe assemblies will be required. The size of the pipe assemblies is related to the size of the switchgear, which in turn depends on the voltage: The support base can be up to 4 metres long for a 145 kilovolt circuit breaker. “Up to 7 pipelines are installed in one circuit breaker”, explains Berge. “In addition, there are customer-specific systems for which we also produce customised solutions at short notice”. HANSA‑FLEX packs the piping for the 230 km transport from the special pipe production facility in Dresden to the Siemens interim storage facility in Berlin Falkensee in space-saving containers specially designed for this purpose. A successful audit proves that all processes run smoothly, from the receipt of the order to the dispatch of the goods.
Innovations on the horizon
“HANSA‑FLEX is an important development partner”, reports Wassermann. Technicians from both companies have got together at numerous workshops in order to jointly push forward innovations. This approach is paying off: “We were able to improve quality by welding the stainless steel pipes instead of soldering them”, says Berge happily. “This is because the flux used for soldering has a corrosive effect, and cleaning is also time-consuming.” The fluid specialist’s know-how is also in demand for further developments, such as circuit-breakers with clean air, a natural insulating medium without SF6 gas.
Perfectly planned
Coordination is always a major challenge with a project of this size, and the tight time frame is another. “Mr Berge and I coordinated the tasks as a twin management team and worked closely with all those involved – even daily during the busiest phase”, reports Wassermann. And even the Covid-19 pandemic has been unable to slow down the project. “From mid-March onwards we only met virtually”, says Wassermann, adding: “But it worked really well.”
Learn more
- 12.03.2024
Fullest confidence throughout Europe
Boels Rental relies on the fast reactions of the Rapid Hydraulic ServiceFind out more - 11.03.2024
Clean oil, clean cement production
How Holcim turns a by-product of pig iron production into a valuable raw material for cement production, and why clean hydraulic oil is indispensable.Find out more