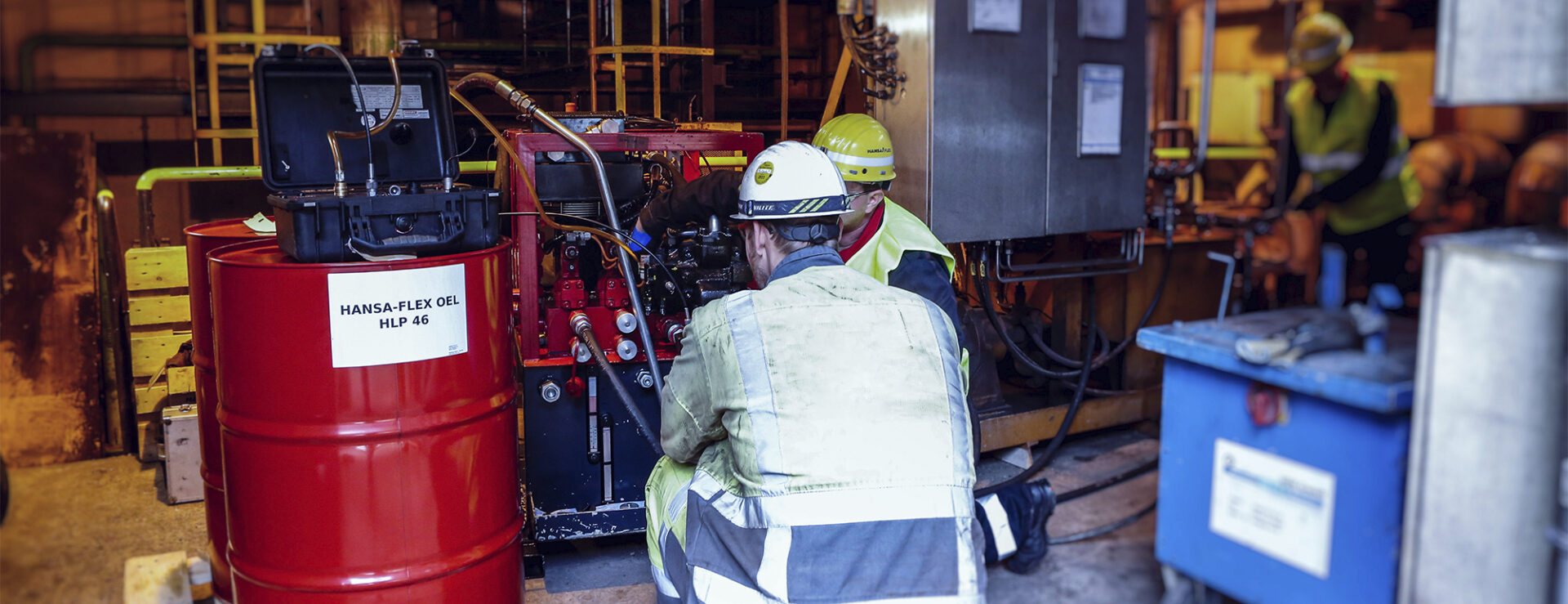
Oil filtration ensures clean fluid and efficient processes
Solid and liquid contaminants cause abrasion, increase wear and promote corrosion. Regular oil filtration ensures your production processes run smoothly and helps avoid damage to equipment, systems and machines. The fluid experts from HANSA‑FLEX perform professional oil cleaning to achieve the desired cleanliness level and find the perfect filter solution for your hydraulic system.
Hansa‑flex fluid service
From hydraulic oil analysis and cleaning right up to fluid-related system optimisation, the experienced fluid experts from HANSA‑FLEX can advise and assist on all matters of fluid management.
On the road with experience and a laboratory
Our fluid specialists take to the road with extensive experience and a mobile laboratory.
Certified quality
Work performed in compliance with the German Water Resources Act (WHG); ISO 9001; ISO 14001 and OHSAS 18001.
Professional damage analysis
We can tell a great deal about the likely damage to hydraulic components from the residues in the oil.
Perfect advice
We advise you on the selection and optimisation of hydraulic systems and fluids.
Why you should carry out regular oil filtering
Prevent machine downtimes and defective components
Avoid oil contamination
Repairs, defective seals or a faulty tank seal can allow dust, and particles of metal or seals to enter the hydraulic system or the oil tank. From there they gradually spread throughout the whole system and damage components such as pumps or valves. The consequences: repairs, failures and long standstills. In addition to regular oil analyses, the selection of the right filter system is extremely important. Whether suction, pressure, return or tank breather filter: there are numerous filtration solutions for a wide range of purposes. HANSA‑FLEX fluid technology experts advise you on their selection, design and installation.
Detect oil contamination
Oils carrying high levels of dirt also carry hidden dangers. Many particles are often invisible to the naked eye. The consequences: even the smallest particles circulating undiscovered inside your system can cause abrasion, wear and corrosion. It is just a matter of time until components appear to suddenly fail. To prevent damage progressing this far, the HANSA‑FLEX fluid specialists analyse the oil on site or in the laboratory. And what if failure has already occurred? As part of damage detection on faulty components such as pumps, motors and hose lines, we make a list of optimisation measures for the hydraulic system, hydraulic and gear oils, which we would be happy to perform for you.
Rectify oil contamination
If foreign material was found from an oil analysis, HANSA‑FLEX Fluid Service can filter the fluid while the system or machine continues to operate. We provide various high-performance filter systems and flushing equipment for hire or purchase. We also design and manufacture flushing units and bypass filter systems individually to suit your specific requirements. These can be a permanent part of your system. Before an oil change and when bringing into first use, our Fluid Service technicians thoroughly flush your system so that no harmful contaminants remain.
Prevent oil contamination
Even fresh oil is not 100 % clean. Residues from production, filling or transport may remain. Levels of contamination may be only slightly better than the specified minimum ISO requirement 21/19/16. This is not adequate for precisely designed hydraulic systems, because even the smallest amount of dirt in the micrometre range can lead to serious problems. Highly-sensitive hydraulic systems in machines and plant engineering equipment require special fluid care. If necessary, the fluid experts from HANSA‑FLEX perform microfiltration of the oil before filling and officially record compliance with the required cleanliness level.
Oil-related services
HANSA‑FLEX Fluid Service carries out oil analyses directly on site, performs oil cleaning or complete oil changes.